MESSAGE FROM THE SMA EXECUTIVE DIRECTOR: Hot Items on the Horizon for the Stucco Industry
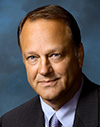
Mark Fowler, SMA Executive Director
I hope everyone is enjoying the transition to Summer. For us in the association world, we tend to already be looking ahead to Fall. It will be here fast, and that is when seminars, classes and various meetings all start back up. This Fall the stucco industry has some challenges and opportunities that could shift the future for all of us. How these issues will impact the overall industry will depend largely on what we do and what we do not do as events unfold. The inaction of our industry is likely to have the greatest impact. Here are some hot items on the horizon.
SILICA: OSHA has dramatically cut the Permissible Exposure Limit (PEL) to respirable silica (RCS). Attending a seminar hosted by CAL/OSHA, many plastering contractors mistakenly believed that plastering had an exemption from the Department of Industrial Relations. The OSHA representation made it clear the exemption was for dust and not respirable crystalline silica. OSHA has the rules on their website www.silica-safe.org and contractors are encouraged to check out the new rules. It should be a wake-up call that the list of trades under scrutiny includes plastering, stucco and EIFS. The SMA has been working hard to develop a “Written Exposure Plan” for stucco. This written plan is required and must be per the tasks specific to the trade. They must also have an assigned person who can explain and implement the plan. Failure to have the plan may result in hefty fines, that increase upon violations. While the White House is predicted to overturn this rule, most feel CALOSHA and other states will keep the more stringent rules in place. States are allowed to make rules more strict than Federal standards, just not weaker.
DRAINAGE: The southeastern U.S. may seem far way for many of us who do stucco in the drier southwest, but actions in that region of the country may impact all of us in the western half of the U.S. There is a code movement to push for a drainage gap behind all reservoir claddings. Stucco is classified by many envelope experts as a reservoir cladding, similar to masonry.
CI: If you are unaware of what CI stands for, you need to get out more often. CI is the acronym for Continuous Insulation. This is the Energy code requirement for a rigid layer of insulation to cover stud framing. Framing has been proven to allow a short circuit in even the best insulated framed walls. Most experts point to Europe as the leader in Net Zero home building. Net Zero is a term to describe the concept of homes that use the same renewable energy they create. It is easier in Europe as they build masonry walls with massive amounts of CI. We tend to use more framing. While it is less expensive, it is also better for seismic zones. Masonry can also be done, but the costs tend to really sky rocket with all the steel needed to comply with more rigid seismic codes.
ONE-COAT STUCCO: The stucco industry has a fire and drainage testing insulated one-coat stucco system. The rigid foam is specifically designed for one-coat stucco with limited thickness and smoke and flame spread requirements. Tongue and groove connections with small drainage grooves on the backside provide for Continuous Insulation to meet Energy Codes and still meet enhanced drainage. The proven non-combustible coating of cement on the outside of the foam should give building owners peace of mind. These systems are 100% code compliant, as they carry an Evaluation Report from the code body such as the International Code Council or IAPMO. One-coat stucco over foam has been proven since 1975 in all types of climates and structures. These proven systems are also very affordable when compared to other claddings. When manufacturers’ recommendations are followed, as per the Evaluation Report’s requirement, they are warrantable and work well for an economical price. The SMA is working on a series of generic details that all one-coat manufacturers can agree on for wider dissemination to the design and contracting communities. Our industry biggest challenge is trained workers.
PLEASE NOTE: SMA OFFICE CONTACT INFORMATION
Mark Fowler, Executive Director
Marlene Lampert, Office Manager
Stucco Manufacturers Association
5753 E Santa Ana Cyn Rd, Suite G-156
Anaheim, CA 92807
Office: 213 379 5890
Mark@stuccomfgassoc.com
Marlene@stuccomfgassoc.com
WELCOME NEW SMA BOARD MEMBERS
DJ Farley of Weatherization Partners and Rick Durham of EZ Concentrate Mix out of Dallas, Texas, have been asked to fill two SMA board positions that became vacant. The SMA board is impressed with DJ Farley’s commitment to the lath and plaster industry. DJ was a lather for several years and brings his experience to the SMA. Rick Durham was a plastering contractor in Texas, and today he is sales manager for the well-known and respected dealer/stucco manufacturer in Dallas. Adams Supply is well known thoughout Texas with yards and products all over the Lone Star state. The SMA is grateful to have Rick provide the Texas connection for the SMA. He will help educate the SMA on regional practices common for the Texas market. Welcome aboard, Rick and DJ.
Our 5TH ANNUAL GOLF TOURNAMENT ON SEPTEMBER 11
The SMA golf tournament will be held on September 11 at the Yorba Linda Country Club. Sponsorships are available for maximum name exposure to your company and product. Contractors and dealers fill the field and have a great day of fun and networking. The dinner and raffle are annual events the stucco industry looks forward to, too.
This year promises to be the biggest field ever as the Yorba Linda Country Club is a private club and only open to outside players through tournaments such as the SMA event. Street tacos will be served at the turn, and there will be lots of fun events. Plan to come and network with the industry on all things stucco.
SAVE THE DATE — NEXT SMA MEETING ON NOVEMBER 8
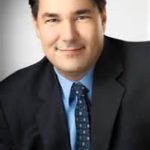
Chris Thornberg is BACK! SMA members have enjoyed Dr. Thornburg’s witty and entertaining presentations on the economy. For those who may not know, Chris predicted the crash of 2008 before most had a clue trouble was on the horizon. What he predicts about the economy could be helpful to you and your business. The meeting is set for November 8 at the Yorba Linda Country Club. Plan to attend — a sellout is expected.
Feature Articles
Apprenticeship in Plastering
An apprenticeship is a system of training a new generation of workers in a particular trade or craft. Classroom and on-the-job training is combined to provide the best results. The level, benefit and length of training depend greatly on the skill required to become accomplished journeyman or journeyperson.
Lathing and plastering may be one of the best examples of where the apprenticeship system has proven to ultimately fail the industry. In the 1950s, construction was booming across America. The war had just ended and there was no greater need for vast numbers of training skilled workers than plastering. Gypsum lath and plaster was a superior finish, but required skilled labor. The plaster was a gypsum basecoat, commonly called “hardwall,” and finished with a skim coat often called the “putty coat.” The result was a durable fire- and sound-resistant wall that could be smooth or textured. By the 1960s, the interior finish coats were pre-blended and even came in various pastel colors, eliminating the need for paint. Within a decade, this superior finish material was all but gone.
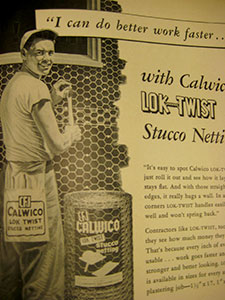
The driving force was increasing costs and loss of workers juxtaposed to a sheet good only needing joint treatment. For plastering to survive, the trade required skilled craft people if production was to stave off the new kid on the block called “drywall.” Drywall required less skill, even mistakes were pretty easy to fix when compared to hard and dense plaster. Drywall was cheaper and faster; the trade off for improved fire, sound and abuse resistance lost out to a cheaper price and lower requirements for training new workers. This should be a lesson to stucco contractors today. Lower priced finishes tend to win out with major market share in the long run. Even in the face of a superior performance, owners will often opt to save money. This explains why stucco is popular in the southwest, where stucco is lower cost and outlasts other claddings by a mile. Prices are impacted by the availability of workers that can install lath efficiently and use trowels in a productive manner. The machine pumps also tend to improve production. But don’t fool yourself — developers will drop stucco if another cladding becomes tempting with significantly lower prices. This has already happened in some parts of the country. We do not want to be a footnote in construction history. Remember, lath and plaster virtually lost the market to drywall in less than a decade.
How do we keep stucco going? Apprenticeship is key. Without a supply of skilled and knowledgeable journeymen who can put up stucco “correctly” with efficiency to keep stucco competitive, we could be in trouble. Failing to train workers could make stucco similar to interior lath and plaster, a very high-end and expensive material only limited to the wealthy who can afford it. What can be done?
We need a national training program for stucco. This sounds easy, as we have established open market programs for electricians, plumbers and even other sidings. But none for stucco. The reason is that the skill and knowledge level for proper lath and plaster application is high. This, combined with the fact that regional preferences and competing groups can never seem to agree on a baseline, can make training almost impossible. The industry needs to come together, put their differences and competition for market share aside to preserve the stucco market. The alternative is to become genuine interior lath and plaster, a limited cladding with a very small to non-existent market share.
Control Joints in Stucco
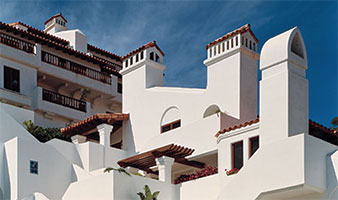
For decades the issue was clear — control joints were not code mandated. It was a designer’s option. This was good, as an architect designing a Tuscan- or Santa Barbara-style home with a smooth trowel finish would certainly find the addition of control joints an aesthetic destruction of his/her design. The SMA agrees that on many projects like these, the occasional hairline crack would be preferred to the control joint. The dilemma today is the code now references the ASTM standards. These standards are clear and they require the use of control joints with specific spacing and installation requirements. The SMA is publishing a paper to provide designers the backup they need to eliminate control joints, if they so choose.
K-Lath Opens New Facility
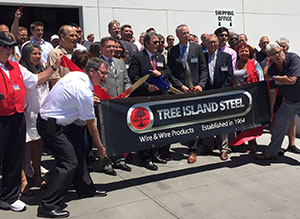
Tree Island Steel has been manufacturing K-Lath for decades. They have grown and kept expanding over those years with innovation and quality for the stucco industry. It was finally decided that putting the operations under one roof just made sense. The massive facility in San Bernardino is a state-of-the-art production center putting out a host of products. Headquartered in British Columbia, Tree Island Steel produces wire, bulk nails, fencing and an array of related products. The San Bernardino facility will focus on lath and the fasteners.
Noteworthy
SMA Office
Most members may not be aware of the phones calls and emails that flow into the SMA office on a regular basis. Most are technical questions looking for help. Office Manager Marlene Lampert has experience in stucco and offers assistance and/or guidance for the more general questions. This is a great asset, as Executive Director Mark Fowler travels quite a bit around the country. Most calls are on painting stucco, why stucco cracks, and is stucco appropriate for various regions of the country. She handles them well. Calls come from around the United States and even the world… calls from Saudi Arabia and Australia are always interesting.
London Fire
The tragic news from England was indeed awful, and our heart-felt concern and condolences go out to England. The video of the Grenfell Tower going up in flames on June 14, 2017, should be a wake-up call to all of us that what we put on the building has tremendous impact to the public. The initial reports on Grenfell indicate the cladding used had an extremely flammable foam core. This is why designers must insure the products they select are code compliant meeting NFPA fire tests and ratings on flame spread and smoke development. The use of rigid foam as a Continuous Insulation will certainly continue; it is likely that more designers and building departments will insist on relevant test data, better protective coatings and designs. Evidence of this trend has already started with a dramatic increase in phones calls on this subject to the SMA office. Cement stucco is non-combustible and proven over rigid foam in fire tests. Remember, there are restrictions to the type of foam used, thickness and the type of cement covering required over the foam to maintain fire resistance. The SMA will be putting out another paper regarding fire and stucco very shortly.