EXECUTIVE DIRECTOR’S REPORT
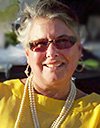
Norma S. Fox, SMA Executive Director
It has been a very good year for SMA. Since we changed to a committee-based association, things are rock’n and rollin’. Ground work has been put in place for new projects and technical papers for us to complete next year. The three coat and the one coat committees have established their guidelines and are hard at work.
For those who participated in our second annual golf tournament … it was a “huge” success. The intense heat broke the day before, and all the players and the rest of us had a big sigh of relief. Our winners were: First Place: Louie Corpolongo, Erik Shimp, Jonathann Shimp and Jared Shimp; Second Place: Brad Stevenson, Don Gilbart, Abel Gonzales and Albert Gonzales; Third Place: Jose Castellon, Walt Niestemski, George Hillman, Dave Ortiz. Closest to the Pin: Steve Heaton and Keith Johnson, Longest Drive Jared Miller, Putting Contest Tony Mastrangelo. Congratulations to all the winners.
I would like to thank all the sponsors and all the member companies that contributed outstanding raffle items. A large portion of the proceeds will go to Wounded Warriors. This will be the fourth year in a row we have contributed to Wounded Warriors. Thank you to everyone who participated and to our volunteers who made the day successful. Let’s do it again in 2015. Put this date on your calendar — September 17, 2015, at Strawberry Farms in Irvine, CA. We will have our membership lunch meeting the day before, so those of you from out of town can attend both in one trip. We do try and accommodate all.
Our quarterly membership meetings have been extremely well attended this year. In fact, we have been sold out for the last three. This is due in part to the excellent work of Gary Alexander in putting together the programs for these meetings. Thank you all for attending and giving us excellent feedback after each lunch meeting. The parking lot at Antonello’s is an excellent place to get that feedback. Again, thank you.
Please remember we have Christopher Thornberg, Ph.D., economist from Beacon Economics speaking again this year. I believe this is his 9th year doing this for us. He is always right on and always entertaining. Don’t forget to register for this lunch meeting ASAP.
Hope you all have a great Thanksgiving and outstanding Holidays … whichever one you celebrate. May 2015 bring you health, happiness and prosperity.
SAVE THIS DATE FOR NEXT YEAR: SEPTEMBER 17, 2015
The SMA’s 3rd Annual Golf Tournament is already scheduled — mark your calendars for September 17, 2015. Don’t miss the camaraderie, don’t miss the fun!
SIGN UP RIGHT NOW: DON’T MISS OUR ANNUAL LOOK AT THE ECONOMY
Learn from our featured speaker, the respected economist Christopher Thornberg, Ph.D. – Join us on November 6 for our annual economic outlook.
FEATURE ARTICLES
Not All Bitumen Flashings Are Appropriate for All Walls
Fortifiber Technical Bulletin – June 2014
In the last ten years, self-adhesive flashings (SAFs) have become the predominant flexible flashing product for windows. Their ease of installation and self-sealing characteristics make them popular in all regions of the country. Rubberized asphalt (RA also known as bitumen) is the most widely used SAF product because of its lower cost. Much has been written about sealant compatibility and installation of RA products (see www.fortifiber.com), but builders are now finding that RA products may not be suitable for all climates.
Product performance, from initial adhesion to long-term softening, can vary depending on ambient temperature and building envelope design. Some manufacturers recommend against using RA flashings in high heat conditions while others are silent on the issue. Fortifiber provides a range of products and encourages product based on the design considerations of the structure.
The temperature of the wall can depend on numerous factors, including (but certainly not limited to) the following:
- The climate and sun exposure of the building elevations (southern, northern, etc.)
- The sheathing material (OSB, gypsum-based, etc.)
- The color and type of exterior cladding (fiber cement siding, wood siding, shingles, stucco, etc.)
- The installation techniques (fastener torque/pressure, sealing of siding joints, etc.)
It’s not uncommon for south-facing walls in hot climates to generate internal temperatures which are beyond the service temperature of many rubberized asphalt products. Fortifiber publishes ‘application’ and ‘service’ temperature ranges for its rubberized asphalt and butyl flashing products. The application range shows the suitable temperature range for initial adhesion of the product (and sometimes a primer may be necessary) while the service range shows the suitable temperature range for the proper long-term performance of the product in a wall system.
Which Flashing Is Right for My Project?
You can generally count on a higher price for a flashing product with a broader temperature range, but extreme temperature climates may demand a more robust product. Mechanically attached flashings such as Moistop neXT and Moistop PF can provide an economical alternative to the more expensive self-adhesive flashings with comparable performance and no temperature concerns.
Visit www.fortifiber.com or call 1.800.773.4777 for information on Fortifiber’s full line of self-adhesive and mechanically attached flashing products and accessories.
Old School Tools for New School Learning
Children Are Born to Build
ConstructionKids introduces new builders to a broad range of materials and tools. We study the natural and man-made world around us, while learning to work individually as well as part of a team. Our goal is to share the joy of building, revising, and repairing.
Real Tools for Small Hands
Our kids work on individual and group projects with real tools and materials that are scaled and selected for small hands. Creativity and problem solving are fostered. If your child can imagine it, we’ll help him/her build it—safely and with the guidance of experienced grown-up hands.
Try a Program
Learn about our after school programs here. We also offer special programs for school field trips, Girl and Boy Scout troops, toddlers, homeschool groups, as well as birthday parties. Contact us, if you’re interested.
About ConstructionKids
Founded in 2009 by Deb Winsor, ConstructionKids developed on the premise that children are curious, capable, and funny. In May of that year, Deb was asked to “build an igloo” with a pre-school class of 4-year-olds in Brooklyn. Following the project’s success, ConstructionKids began to grow, and expanded into a full-blown professional workshop where children are taught how to use tools and learn how to build – among other things – go-carts, buildings, mazes, bridges, and musical instruments. Once housed in Deb’s playroom, ConstructionKids now offers programs in three New York City locations. Its flagship location at BLDG92 in the Brooklyn Navy Yard boasts some 2,700 square feet of workshop space for its students. Contact ConstructionKids to learn more.
Best Practices for Selection and Installation of Expanded Metal Lath Products
ClarkDietrich™ Building Systems, White Paper – January 2014
SPECIFYING THE APPROPRIATE METAL LATH PRODUCT for the application and installing it properly has a dramatic impact on the long-term stability of a building’s exterior cladding. Fortunately, there are various building codes and industry standards that are excellent guides to best practices for product specification and installation. The purpose of this article is to take a closer look at the aforementioned codes and standards and their recommendations for selecting and installing the best-quality expanded metal lath products for specific applications—in addition to highlighting common installation errors and their consequences. As such, we hope to provide project teams with a resource that will help them produce more stable, long-lasting exterior wall assemblies.
Introduction
For more than 50 years, expanded diamond-mesh metal lath has been regarded as an integral component of stucco building exteriors, which consist of cement or gypsum plaster applied over wood or gypsum sheathing. At first glance, it appears to be a fairly simple material, and very few changes have been made to its manufacturing process over the years. However, the expanded metal lath product specified and the way it is installed has a huge impact on the long-term stability of the plaster it supports.
Specifying Quality Products
Like all other building components, selecting and specifying the right product greatly reduces the potential for job failures. With such high stakes involved, it is important to ensure that the specified product has first been examined and tested by an accredited third-party certifying body to verify its compliance with the International Building Code (IBC), the International Residential Code (IRC) and the industry standards they reference. The industry standards most widely used by the IBC and IRC to gauge the product performance needed for code compliance are: ASTM C847, Standard Specification for Metal Lath; and ASTM C1063, Standard Specification for Installation of Lathing and Furring to Receive Interior and Exterior Portland Cement-Based Plaster. Appropriately, the measure of an expanded metal lath product’s quality begins during the manufacturing process.
Manufacturing to ASTM Specifications
In general, the manufacturing of expanded metal lath begins when a small (< 12 inches) G-60 galvanized steel coil (meeting ASTM A653) is gradually uncoiled and fed into the cutting rollers of a large rotary expanding machine. The cutting rollers apply a force of more than 100,000 pounds (445 kN) to slice through the sheets, creating the diamond configuration. Stretcher arms on the machine attach to the coil and expand the sheet into compacted diamond-pattern sheets, 27 inches (696 mm) in width. The machine will have a sheet end cutter that can be set to various lengths—typically, 97 inches (2,464 mm) is the minimum length for packaging as a standard sheet, per ASTM C847-10 requirements. Manufacturers are required to maintain cutting rollers to ensure clean cuts and prevent formation of unexpanded diamonds or the fracturing of diamonds in configuration (see photo left).
Self-furring laths require an additional step in the manufacturing process: the machine embosses the sheet with either dimples or V-grooves, providing 1/4 inch (6.4 mm) of furring, measured from the back of the dimple or groove to the face of the lath strands. The furring tools are monitored by the manufacturer, as worn tools can cause a sheet’s furring to fall below the 1/4-inch length required by ASTM C1063. If the tools are found to produce furring below the required length, they are replaced.
Alternate Metal Plaster Bases
One commonly used expanded metal lath material is welded wire, produced to ASTM C933, Standard Specification for Welded Wire Lath. This welded wire lath can be manufactured self-furred, thereby providing full embedment of the plaster scratch coat, which is ideal for expansive wall panels where the stucco will be machine applied, or sprayed. Another lesser wire material is woven wire, more commonly known as “chicken wire,” which is produced to ASTM C1032, Standard Specification for Woven Wire Plaster Base. This product is typically used on single-story mass-production housing and usually has to be furred to the substrate.
Building Code Requirements
The IBC and IRC call upon ASTM C847 to define the expanded metal lath product’s physical properties required for code compliance. This standard lists minimum lengths, widths, lath thicknesses and weights for products, as well as allowable tolerances. In order to meet these criteria, metal lath manufacturers have to pay close attention to a variety of details in their product design, including: the base thickness of the galvanized steel coil, cutter configurations and the pull force applied to the galvanized steel coil while being stretched. ASTM C847 calls for metal lath to be manufactured from cold-rolled carbon steel sheets, per ASTM A653, Standard Specification for Steel Sheet, Zinc-Coated (Galvanized) or Zinc-Iron Alloy-Coated (Galvannealed) by the Hot-Dip Process. In addition, ASTM A653 requires hot-dipped galvanized lath to have a coating of at least G-60, signifying a zinc content of 0.6 ounces/square feet (183 grams/square meter).
While the minimum galvanized coating required by ASTM C847 is G-60, it is possible to use other materials to protect metal lath from corrosion. One example of this is increasing the galvanization to G-90—where zinc content rises to 0.9 ounces/ square feet (274 grams/square meter)—or using pure zinc alloy (99 percent pure zinc) protective coating.
Expanded Metal Lath Accessories
The accessory material selected for a particular expanded metal lath application depends largely on the climate of the building’s location, along with the type of plaster/stucco or stone application used to form the façade. For instance, the higher humidity and salty air of coastal environments often demands a higher zinc alloy, or possibly PVC, for exterior skin components. However, in drier climates, galvanized accessories are more acceptable. Specifiers should note though, there may be trade-offs with certain materials. For example, while zinc alloy offers greater corrosion resistance, the material is considerably softer than galvanized steel. And, while PVC accessories are non-corrosive, they may not fit the building owner’s aesthetic preferences. Another important thing to remember is that grouping incompatible materials in the final specification of lath, fasteners and accessories can increase the possibility of galvanic corrosion (i.e., electrolysis) or inconsistent corrosion protection, which threatens the stability of the building’s cladding.
The specifier and installer should be aware that physical characteristics of lath products being installed fully comply with ASTM C847-10 requirements. Examples of these “below-code” characteristics are lath weight, length, width and low galvanization (i.e., G-40). Products with the markings of “utility” or “nominal,” should be avoided for use in inspected facilities or code-compliant construction. The negative effects of lesser galvanizing and lath weight are quite apparent—below-minimum zinc coatings invite corrosion, while lower-than-minimum lath weights can compromise the building exterior’s resistance to structural and wind loads. However, the effect of shorter lath lengths may not appear so obvious at first glance. Lath sheets are traditionally manufactured in 97-inch (2,464 mm) lengths to accommodate framing member spacing of 16 or 24 inches (406 or 610 mm) on-center, with an extra 1-inch (25 mm) end lap stipulated by ASTM C1063, Table 3. Simply put, use of 96-inch (2,438 mm) long sheet lath over standard framing member spacing will not provide the specified lath overlap, which, as a result, can cause cracking through the stucco finish.
Proper Installation Is Key
Proper lath installation is of equal importance to the longevity of plaster-based building exteriors. Below are some of the most common lath-related installation errors and how they can be avoided.
Improper Plywood Sheathing Installation
According to the American Plywood Association, plywood sheathing should be installed with a minimal gap of 1/8 inch between sheets to accommodate any expansion that may occur in the wood as a result of moisture intrusion. It is important to note that in any case where large amounts of moisture enter the exterior wall assembly, the plywood may delaminate or swell significantly, ultimately causing the stucco cladding to deteriorate. The best protection against these liabilities is an effective moisture management strategy within the exterior wall assembly, consisting of high-performance insulation, air barriers and vapor retarders or barriers.
Improper Installation of Water-Resistive Barriers
Chapter 25 of the IBC—“Gypsum Board and Plaster,” Section 2510.6-Water-resistive Barriers”—states that exterior wall assemblies shall include two independent layers equivalent to Grade D paper that serve as water-resistive barriers. The only exception is the use of 60-minute Grade paper and a non-water-absorbing layer drainage plane, or rain screen.
Improper Metal Lath Installation
Some of the more severe metal lath installation errors involve improper lapping attachment to the framing members, improper installation of paper-backed lath, incorrect fastening of the adjoining sheets at the laps and the improper orientation of the lath sheets. A well-defined installation primer for laths with or without paper can be found in ASTM C1063, or the Expanded Metal Lath Association’s Guide Specifications for Metal Lathing and Furring (EMLA 920-09) and can guide the contractor toward a successful installation.
Improper Fastening of Metal Lath
Improper fastening of metal lath is the most common installation error and is often a result of the lath being randomly stapled or nailed to the sheathing instead of the structural member. ASTM C1063 requires lath fastening at minimal intervals of 7 inches on-center. Lath accessories’ flanges must directly touch the lath, with no weather barrier sandwiched in-between.
Improper Installation of, or an Inadequate Number of, Expansion & Control Joints
ASTM C1063, Annex A1.2, defines control joints as one-piece joints used to provide crack control for stucco shrinkage, drying and thermal expansion. The same standard describes expansion joints as two-piece joints used to accommodate some degree of movement in the stucco membrane caused by movement in the building or its components. Fastening the expansion joint flanges to sheathing, or leaving the lath un-cut behind the joint, negates the lath’s effectiveness. Just like all accessories, the expansion joints must be wire-tied to lath edges or, in some applications, attached to supports at spacing that ensures stability. On large, vertical surfaces, it is wise to make vertical joints continuous and cut horizontal joints to abut the verticals, with proper care taken to prevent the horizontal joints from impeding the vertical joints’ movement.
Improper Installation of Flashing or Sealants at Potential Points of Water Entry
Any poorly installed or omitted flashing in areas where water can enter the exterior wall assembly can easily cause the cladding, sheathing and wood framing members to deteriorate. Mold growth may also result from extended moisture exposure, causing indoor air quality problems inside the building. Though flashing is generally not the responsibility of the lath contractor, lath contractors are advised to notify the general contractor if they see improperly installed flashing or areas where flashing was left uninstalled.
Conclusion
In order to provide customers with high-performance, long-lasting building exteriors and minimize liabilities, it is imperative for building and design professionals to be well informed of all applicable building codes and ASTM standards. Adherence to the guidelines covered in this paper will produce healthier, more stable and sustainable buildings and reduce callbacks to a minimum.
About ClarkDietrich™ Building Systems
ClarkDietrich™ Building Systems is the leading manufacturer of a full-line of drywall studs and accessories, structural studs and joists, metal lath and accessories, shaft wall studs and track, interior finishing products, and connectors and accessories for commercial and residential construction. Quality manufacturing, a full-line offering, national distribution, engineering services and responsive customer service position ClarkDietrich Building Systems as the largest and fastest growing manufacturer of cold-formed steel framing in North America. Clarkwestern Dietrich Building Systems LLC is a 75/25 joint venture with Marubeni-Itochu Steel America Inc. (MISA) and Worthington Industries, Inc. For more information, visit www.clarkdietrich.com. Vinyl Corp™ is a wholly owned subsidiary of ClarkDietrich Building Systems™, dedicated to extruding the finest quality PVC components for the wet-wall and drywall trades, including stucco & plaster, EIFS/DEFS and drywall. For more information, visit www.vinylcorp.com.
Cost Containment, Talent Acquisition Top Benefit Challenges
Executive Perspectives – August 2014
A recent survey by Arthur J. Gallagher & Co. reveals that employers continue to see rising benefit costs in 2014. In excess of 1,800 U.S.-based organizations participated in the survey spanning a wide range of industries, geographic regions, and employer sizes and types. The majority of participants (61 percent) have more than 100 full-time employees and 25 percent of participants employ 500 or more full-time employees.
The two biggest challenges identified by these participants are the need to control benefit costs while attracting and retaining a competitive workforce. The survey, conducted by Gallagher’s Employee Benefit Consulting and Brokerage operation, examines how organizations are responding to healthcare reform and rising costs, as well as their approach to private exchanges, wellness and retirement programs, and other benefit trends and opportunities. Employers can leverage the insights from the survey results to effectively make near-term decisions, as well as guide their long-term strategic planning.
“Although organizations may be aware of the changes that are shaping the future of the employee benefits market, the survey suggests that many are not yet ready to face the challenges these changes will bring,” said James W. Durkin, Jr., President, Employee Benefit Consulting and Brokerage. “Those that adequately adapt to the current reality will optimize their ability to mitigate future costs.”
Controlling Costs
When asked to identify their greatest overall challenge, 67 percent of employers cited controlling benefit costs. Some of the leading strategies identified by the participants for containing benefit costs include:
- Increasing employee plan contributions (54 percent)
- Increasing deductibles (43 percent)
- Increasing out-of-pocket maximums (36 percent)
- Increasing copayments (30 percent)
Attracting and Retaining a Competitive Workforce
Given today’s dynamic workforce, employers are seeking to balance cost containment with employee engagement. Moreover, the increasingly diverse needs and preferences of the current workforce challenge employers to develop a benefits package that appeals to all employees. Survey results show:
- Retirement plans continue to shift toward a defined contribution model, with 64 percent of respondents offering a 401(k) plan.
- Of those, 70 percent match employee contributions.
- Employers continued to gravitate toward wellness programs with 44 percent of participants offering a program to their employees.
- However, even with the increase in the number of employers offering a wellness program, most programs (61 percent) have a budget of less than $10,000.
- Although employees are often interested in long-term care as a voluntary benefit option, 82 percent of employers do not offer this benefit.
Conclusion
U.S. organizations of all sizes and types are looking to contain healthcare and other benefit costs, while competing successfully for talent. However, in today’s uncertain environment and ever-evolving employee regulatory landscape, only 31 percent of employers surveyed have quantified the cost impact of healthcare reform on their organizations. Just 10 percent of participating employers have a written total rewards or strategic benefits plan with measurable objective.
“There is no doubt that the changing benefits landscape will present organizations with complex challenges for years to come,” said Mr. Durkin. “A holistic, innovative, data-driven employee benefits strategy is needed to strike the optimal balance in managing the best interests of employees and employers. This approach allows organizations to respond to change with agility, helping them to minimize risk, maximize rewards and drive growth.”
Reprinted from Executive Perspectives: What Today’s Business Owner Needs to Know, from Pacific Coast Benefits Insurance Services, LLC. Phone 406.847.1000 or email dave@pacbenins.com.
PRESS RELEASES FROM OUR MEMBERS
Dave Feitl Joins Rhino Linings Corporation as Director of Sales for Building Products Group
Rhino Linings Corporation has named Dave Feitl director of sales for the company’s building products group.
In this newly created position Feitl will oversee both the sales and technical functions of the Concrete Solutions®, Expo Stucco™ and spray foam insulation, sealant and roofing product lines.
“In just a few years, we have expanded our building product lines exponentially,” said Pierre Gagnon, president and CEO of Rhino Linings Corporation. “We want those product lines to be as successful as our elastomeric products, and we needed someone focused exclusively on growing that area of our business.”
Feitl brings years of experience in the building products industry to the job, with a particular emphasis on spray foam, sales and product development. He spent eight years in various jobs at Demilec USA including national sales manager and chief operations officer. Since then, Feitl has held key executive positions at Duna USA and most recently senior vice president of marketing at Thermal Products Research.
Rhino Linings Corporation made a name for itself in the truck accessories market as the leader in sprayed-on truck bed liners. In addition to its well-known vehicle protection, elastomeric and specialty coatings product lines, Rhino Linings Corporation has expanded into the building and construction markets.
Rhino Linings Corporation offers a suite of building solutions for architects, builders and homeowners with its Concrete Solutions® repair and decorative concrete overlay products, BioBased Insulation® and DuraTite® spray foam insulations and Expo Stucco™ exterior stucco products, plasters, interior finishes and patching products.
For more information about any of the products offered by Rhino Linings or to learn more about becoming a Rhino Linings applicator, visit www.rhinolinings.com.
About Rhino Linings Corporation
Rhino Linings Corporation, established in 1988 and headquartered in San Diego, California, is a privately-held corporation and world leader in protective coatings and linings. Products manufactured and distributed by Rhino Linings Corporation include polyurethane, polyaspartic and epoxy coatings, concrete coatings, spray foam insulation and sealants, and interior and exterior stucco. Rhino Linings Corporation has a global retail and industrial applicator network consisting of more than 2,000 independently owned and operated businesses in almost 80 countries and is the first company in the sprayed-on bed liner industry to achieve ISO 9001 certification. For more information about Rhino Linings Corporation, call 858.450.0441 or visit www.rhinolinings.com.
Merlex Stucco Introduces LEVELX to Their Product Line
Merlex is pleased to offer LEVELX – a polymer modified leveling and base coat specifically designed to level different wall substrates and provide a crack-resistant base coat. LEVELX contains a high percentage of polymer for flexibility and bond strength, and additives for workability and working time. The product has suction to ensure good bond between the finish plaster and base coat. LEVELX can also be used on rescrubs directly over structurally sound existing plaster, eliminating the need for sandblasting. When mesh is embedded in LEVELX, cracking is reduced significantly, which allows for higher-quality smooth-troweled finishes, or for any finish when crack tolerances are low. For more information please call 714.637.1700 or visit online at www.merlex.com.
Merlex Stucco Expands Its Portfolio into Panama
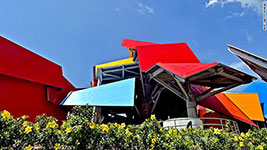
Merlex is proud to be a part of the biodiversity museum, known as Bio Museo, which officially opened its first phase on October 2, 2014, in Panama. Designed by Frank Gehry and plastered by H.I. Homa with consulting from Tom Crow of Crow Plastering, Bio Museo is an exhibition space and botanical park which highlights Panama’s natural wonders and its role as a geological bridge between two continents. With its vivid appearance seen along the canal’s eastern gateway, the stucco facade captures the feel of its surroundings.
Parex USA Announces New Leadership Structure
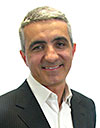
Parex USA, Inc., a leading building material manufacturer which markets its product under the brands of Parex, LaHabra, Merkrete, Teifs and El Rey, announced the promotion of Rodrigo Lacerda to President of ParexGroup Americas, and the addition of James Chilcoff as Managing Director of Parex USA.
As President of ParexGroup Americas, Lacerda will supervise all the Group’s companies in North and South America and will continue to be part of ParexGroup’s Executive Committee as Senior Executive Vice-President. In his new role, Lacerda will coordinate the growth of the group on the North and South American continents and insure the company continues to develop sound strategic positions in each of the countries where we are present.
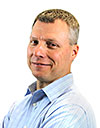
Chilcoff, the new Managing Director of Parex USA, has had a successful career in the Building Materials industry. He previously spent twelve years with James Hardie in various Sales, Marketing and General Management roles, including in Australia, where he led the company’s operations. More recently, Chilcoff was the Managing Director of U.S. Gibraltar Industries, a leading manufacturer of metal and flashing products. Chilcoff has a BA in Marketing from Eastern Michigan University and a MBA in Management from Xavier University.
About Parex USA
Parex USA, Inc., a California Corporation, is a subsidiary of the ParexGroup, one of the world’s leading manufacturers of specialty chemicals and ready-to-use mortars for the construction industry. With over 61 manufacturing sites and 9 R&D centers in 21 countries, the ParexGroup employs more than 3,550 industry professionals who are the corner stone of this thriving global organization. For more information regarding Parex USA, Inc. visit www.parexusa.com.
Atlas EPS Adopts New Evaluation Agency
Atlas EPS is pleased to announce formal evaluation listing with Underwriters Laboratories (UL). The new evaluation report (UL ER16529.1) is a direct comparison to the traditional ICC-ES evaluation report that has been standard for the industry. Atlas EPS has long relied on UL for 3rd party approval auditing and classification listing, and is confident the new UL evaluation report will enhance Atlas’ reputation of providing code compliant building materials.
“With competitors to ICC-ES emerging in the code evaluation field, UL seemed to be a better fit for Atlas EPS, given their strength in fire safety and material compliance,” according to Ted Grant, Technical Services Director at Atlas EPS. “We made the change with careful consideration of the reputation of UL for code compliance. Clients should be assured that products marked ‘ER16529.1’ will be readily accepted by code inspectors.”
The new UL report includes approvals for exterior walls of commercial buildings (NFPA285 approvals), products exposed in basements with no drywall, R-value enhanced Neopor products, and water resistive barriers. These applications are not “prescriptive” in the codes, and the evaluation report instructs the inspectors of how the products have passed ASTM, ICC-ES, or NFPA criteria to prove suitability.
Atlas EPS continues to be the leader in the EPS industry for approved products in all areas of building construction. In addition to the evaluation report, Atlas EPS continues to use Classification Listings with UL for UL723 (E84), C578, E2430, D6817, UL790, and UL263 (hourly fire ratings). FM Approved products are also available.
About Atlas EPS
Atlas EPS, a division of Atlas Roofing Corporation, specializes in the development and manufacture of innovative, high-quality, HFC- and HCFC-free Expanded Polystyrene (EPS) insulation for construction, packaging and OEM products. Headquartered in Byron Center, Michigan, Atlas EPS maintains four locations in North America. Its molding facility in Michigan is the largest EPS manufacturing plant in the industry. For additional information about Atlas EPS, visit atlaseps.com or call 800.917.9138.