MESSAGE FROM THE SMA EXECUTIVE DIRECTOR
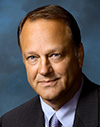
Mark Fowler, SMA Executive Director
TAKE A VACATION: Summer is here, and I hope all SMA members take some well-deserved time off and enjoy a relaxing vacation. This should be a strong message to all owners and supervisors as well. Stress levels are increasing in everyone’s life. It is the sign of the times. The stress you feel today is more than you felt last year and much more than you had a decade ago. The forecast for next year is the stress level will likely increase again. This makes vacation time not just a nicety, but paramount. Talk to your employees. too.
Turn off the phone, leave the laptop at the house, and enjoy your family. De-stress and re-charge. Business owners have a really hard time doing this. It is hard to blame them, as they worked hard to build a successful company and often spend sleepless nights and fear things will go wrong while away. But you are of no value to family if you are dead. Maybe I’m being a bit too blunt, but stress is a killer — ask any cardiologist. So please, take some time to unwind and relax … if not for yourself, then for the ones who care and depend on you. TAKE CARE OF YOURSELF.
DO WE NEED CHANGE?
The SMA is growing in size — and influence. Just in the last year the SMA has helped several city inspectors, designers and many others in states across our great country. This is because lathing & plastering are skilled trades. They require knowledge of materials and the craft to properly advise and lead the industry. Simply quoting ASTM or handing out a checklist is inadequate for designers, inspectors or developers looking for qualified answers and they want third-party unbiased answers. Plastering is not drywall — and mistakes cannot be easily sanded away. Mistakes in stucco applications can lead to leaks, excessive cracking and potential litigation concerns. We seem to have forgotten our roots of plastering.
Blending semi-skilled trades with the more highly skilled crafts leads to an inevitable decline and dilution of the more skilled craft. This is because cost drives most everything, and developers typically select the lower cost options. This is evident by the loss of interior plaster to drywall. As drywall grew, interior lath & plaster became increasingly more irrelevant. When bundled in large trade groups, the majority wins and plasterers lose. This is actually fair and democratic. The more skilled craft, like lath and plaster, needs more training, education and attention: all this costs money. Since all big entities run on money, lath & plaster can look like a drain on resources to many of these groups.
It also explains why highly specialized trades develop their own national group. A group that focuses only on poured-in-place terrazzo has discovered this fact. They know it is only the highly skilled craft that can command a higher installed price than the cheaper alternatives. This product, like plaster, commands more education and a cohesive industry to work together for one goal, more market share through quality and excellence. This also includes promotional budgets to get the word out to the design community.
The SMA knows better than most: designers and building owners want lath, plaster and stucco. They will even pay a slight premium for it. They are simply confused on how to detail, specify and where to turn for true third-party expert advice. Telling them to go to ASTM or handing them a checklist is not going to get the job done.
The lath and plaster industry has other issues too. We are conflicted. Various groups have opposing opinions and these conflicts create dissention and make our industry an easy target to attack. Most big wall and ceiling contractors seem content and even encourage to let stucco and plaster die. They are businessmen and know that it is better business not to be required to hire specialists, like lathers and plasterers. In the growing Design Build world, these contractors will push for metal panels or claddings other than lath & plaster. It is smart business for them, but not for us.
Most terrazzo specialists can do tile work, but have either quit or opt to avoid this if possible. They tell me that making money on tile is hard. It is a commodity-driven business that relies on high volume with low profit. Similar to drywall, money is made by units sold and leveraging your capital to maximize your return on investment. All agree that they can make more profit on poured-in-place terrazzo with lower volumes. They just need skilled, productive workers and well-educated supervisors. Terrazzo is a high-end, long-lasting product and not a commodity item installed by the semi-skilled. Doesn’t this sound like plastering? They know terrazzo requires dedicated promotional efforts to the design community, a pool of skilled labor, educated supervisors, a single-source entity for standards and authority. While the terrazzo industry is small, it is strong, profitable and growing. They broke away from their cheaper cousins and set out on their own path, free of conflicts to determine their own future and not to be a sideline business in a mega-semi-skilled corporation.
Uniting could lead to a stronger, more profitable and expanding plaster market. The desire by the design community and owners is already there — they want plaster and stucco. The industry just has to find a way to unite, remove regional conflicts and position plaster as a premium product through quality and expert influence. The goals are ambitious, the tasks are hard, but end results could be worth looking at our industry from a different perspective.
TECHNICAL COMMITTEE
Contractor members are part of the L&P Committee [contractors: click here if you’re not yet signed up] and are invited to participate in the SMA Technical Committee. The SMA Technical Committee is a forum to discuss and find solutions to technical issues facing the plaster industry. This committee develops details and technical papers that will help shape the direction of the lath and plaster industry. If you are not the proper person in your organization to join, then pass this information along to the person who can contribute to the Technical Committee.
SILICA — OSHA STARTS CITATIONS
OSHA has released its first six-month report of silica exposure violations. They have issued 117 citations, and most were rated “serious” in nature. The top three violations were:
- Not having a written exposure plan
- Not following Table One
- Failing to have monitoring data when deemed needed
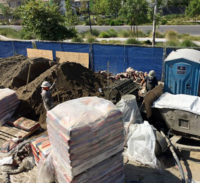
The SMA has items 1 and 3 covered for SMA contractor members. As a part of the SMA’s Silica Compliance Program, you will have a written plan tailored to stucco and adhered masonry work. This includes mixing mortar. The SMA has continually been monitoring silica exposure, and you are using “Industry Objective Data” as your monitoring requirements.
The SMA now offers Competent Person training to all members online, at no charge. Contact the SMA if you are interested in having a class. The SMA is also working on new and improved engineering controls for silica exposure through our continued monitoring efforts. [Click here if you need additional information about the SMA’s Silica Compliance Program.]
PROMOTING STUCCO
The SMA has been busy with architectural presentations and even visited a few large general contractors around the country to promote stucco. We are working jointly with our labor friends to promote stucco. The SMA budget for promotion is small, so more members mean more budget and more promotion. Help bring others in to help the stucco market grow. After all, cement plaster/stucco is a low maintenance, durable and cost effective cladding for the life cycle of a building.
SAVE THE DATE: SMA GOLF SEPTEMBER 24, 2018
The SMA’s annual golf tournament will again take place at the private Yorba Linda Country Club. It is always a well-attended event, and sponsorships are available in Gold, Silver and Bronze levels. Your sponsorship provides name recognition for your company and helps the SMA grow to promote a stronger stucco market. Online sign-ups coming soon.
Feature Articles
PERFORMANCE GRADE, PERFORMANCE CLASS AND DESIGN PRESSURE
The SMA recently presented a short class on Windows and Water Testing. While you might think “what is it and why should I care,” you might want to give it some thought. Evidence of this is when a few attendees came up after the class and express interest. This is because they are currently in a litigation case and watching water testing being applied to their stucco projects. A real-life example was presented where a national building envelope firm had designed and then tested for leaks. Most plastering contractors have no idea of the rules and protocols to water penetration testing. The SMA example clearly demonstrated the firm was not following proper protocols and procedures. The first and most clear evidence was the building envelope firm self-performed the water testing. The American Architectural Manufacturers Association is very clear that testing is only valid when done by an AAMA lab. They are true third-party, trained and use calibrated equipment. The rules can be complex — some experts may be testing fairly or they may be interpreting, tweaking or even making up the rules to fit a desired out come. If you play a sport, you know it helps to know the rules. Why would it be any different for water testing and your business? Knowing the rules can save you a lot of money.
WHY WATER? The experts will almost always drift to water testing. The more seasoned and experienced at litigation, the more they push for water testing. If you misplace a fastener and technically violate the code, the ultimate question is, will it cause damage? If you have damage, your insurance must pay. Water causes damage, even a tiny, slow and continual leak will cause damage. Is there anything you can do to protect yourself early on? While no one can guarantee you will not get sued, some knowledge and protective action can help protect you, your builder and the architect to better buildings and save everyone a lot of grief down the road. This is needed because unjust litigation does occur.
DESIGNERS: Plastering contractors are not designers and are advised not to take on that role. However, you can and should ask the designer for clarification and can even provide them information to better protect yourself and them. Handled properly, an architect will be grateful for the help. Architects have a daunting task: they must design to meet code, select products and assemblies that are appropriate, sustainable and stay within budgets. They cover electrical, plumbing, fire, sound, concrete, structural issues and a plethora of other design issues. They cannot be expected to be experts at every single discipline to design and construct a structure. It is just not possible in today’s complex world. They also have liability issues that can be significant, with repercussions that could result in a loss of their license, effectively putting them out of business.
COMPONENTS & CLADDINGS: A building is a mass of puzzles, pieces, codes and standards. Compliance is daunting to say the least. Most issues on building for the specialty contractor are very limited to their scope. But the specialty contractor should be an expert at his trade and have a working knowledge of all items that touch his/her trade. Architects must deal with the Components and Claddings section in the code. This requires architects to design a structure to meet established Design Pressures per a formula in the code. This is typically established by the Engineer of Record as a positive and negative wind pressure as it relates to stucco and windows. Since windows touch stucco and seem to have leak issues, it might help to know just a bit about windows and water testing. The architect is supposed to select windows, doors, decks and anything that interrupts the cladding based on this pressure. That is why what window works in Phoenix, Arizona, may have no relation to what is required in Miami, Florida. The cladding itself must be approved and how it is fastened to the structure to meet these criteria.
Fortunately, generic stucco claddings meet requirements, other proprietary claddings must have an Evaluation Report. Windows are tested rated in performance classes from Residential (R) to Architectural (AW) grade. Some architects are not well versed at design pressures and performance grades and fail to specify products suitable to the structure. Some developers will switch out products to save money by using a lower-rated product. In addition, different areas of the building can have different pressures, and windows can be put in the wrong place. The end result is that windows not rated for the location will leak, and too often stucco gets blamed.
It is not a bad idea to ask the general contractor if the window’s performance grade meets or exceeds the structural engineer’s wind loading to insure proper flashing and integrating the windows and your stucco siding. This is simple and does not make you a designer, but can alert the architect and general that we all need to be vigilant. The chart above, labeled AAMA/NWWDA 101/I.S.2-97, helps explain grades and pressures and illustrates not all windows are created equal.
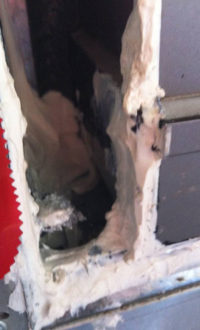
PASSED THEN FAIL: Another common issue is to have a design and construction team build and test with extreme water pressure on site. This gives everyone a sense of security that they will not get sued later. Then eight years later, the contractors are informed they are being sued for water leaks in and around windows in the stucco. How can that be? We tested at even higher pressures, they passed, but now leak?
The clue is that oftentimes you hear, “we never passed the first water test. But we work until it passes.” This can mean that blobs of sealant are continually added at leak points during the test until it passes the next test. The problem is that eight years later, those blobs have failed and water can now get in even under low pressure. The sense of security can disappear fast. The inset picture is one of those examples. The envelope firm on this project is nationally known and highly respected, yet the flashing was complex, poorly designed and simply not constructible. Water intrusion was obvious on the first few tests. However, with enough sealant smeared at just the right place(s), water is kept out, at least for now.
STUCCO AND CORNERS
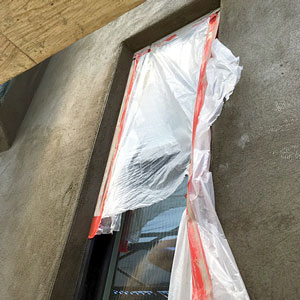
This may be one of the most important items a plastering contractor can read. You must match your corner trim accessory to the finish coat and the environment you are working on. The SMA routinely receives calls on corner issues and stucco. The most common is the rusty corner. The picture of the inset window in the cement brown coat is typical. One can see the nose of the corner aid vertically along the left side of the window. This is common and by itself not an issue. The aid is galvanized and will resist rusting. ASTM notes the aid shall be covered by 1/8 inch cement, traditionally accomplished by the addition of the cement finish coat. Compliance met and it works. However, acrylic finish coats have become very popular. They hold color better, they offer some flexibility and look great.
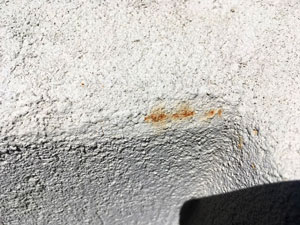
However, they can hold moisture in longer than then 1/8 inch of cement. In wet or very humid conditions, rust spots can occur on the corners when a galvanized nose aid or bead is in contact with acrylic or elastomeric coating. The solution is to use PVC nose corners when using an acrylic finish coat where the structure is going to be exposed to constant humidity. This is why PVC nose is popular in Florida and Seattle.
Another option often discussed is to bury the nose of the aid/bead in 1/8 inch cement brown coat. This makes little sense. The corner trim is a guide for the plasterer to use. The nose will naturally be exposed by the rodding of the brown coat to insure a flat and true plane. To add brown coat back will defeat the purpose of the procedure to rod the wall in the first place. The answer is to use a PVC nose on acrylic finish coats over cement plaster. I am certain many plasterers can swear they use metal nose all the time with acrylic finish and never have an issue. That is likely because the corner is not in a humid environment.
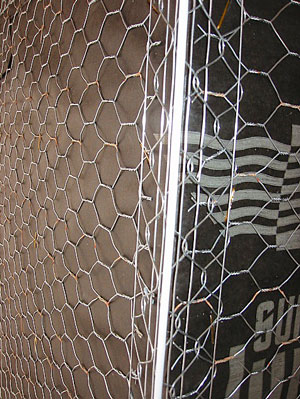
PVC NOSE: Some contractors in humid regions feel that using PVC nose 100% of the time on all projects is the solution to all their problems. That would seem to make sense, except there is a catch and a whole new problem arises when a cement finish coat is selected. The PVC nose will allow the cement finish to stick. However, over time the cement will pop off. The PVC will expand and contract, but cement will not. The PVC corner can flex, but the cement cannot. Acrylic finish expands and contracts with the PVC and flexes when it moves through structural deflection or impact.
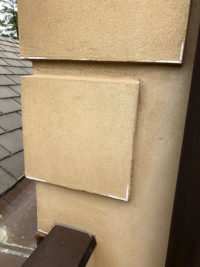
The plastering contractor is considered by the legal system to be the expert at his/her craft. Even if the architect specifies the wrong nose for the finish or the project, responsibility will generally fall onto the specialty contractor’s area of expertise and the failure to notify the designers of well-known practices by the industry. The following is recommended by the SMA.
- Use galvanized metal nose for cement finish coat stucco.
- Use PVC nose for acrylic finish coats over cement brown coats in regions with high humidity.
- Notify the architect or owner you prefer to follow SMA recommendations. Proceed as directed by design team or owner.
PLEASE NOTE: SMA OFFICE CONTACT INFORMATION
Mark Fowler, Executive Director
Marlene Lampert, Office Manager
Stucco Manufacturers Association
5753 E Santa Ana Cyn Rd, Suite G-156
Anaheim, CA 92807
Office: 213 379 5890
Mark@stuccomfgassoc.com
Marlene@stuccomfgassoc.com
REMEMBER: The SMA has a fairly large library on all things stucco. Members of the SMA are encouraged to call the SMA office if the staff can be of any assistance.