FROM THE SMA EXECUTIVE DIRECTOR
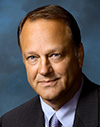
Mark Fowler, SMA Executive Director
I think it is fair to say that 2020 sucks, and we cannot wait for it to end. The SMA hopes we can go back to normal sometime in 2021, but even that is not guaranteed. I run two national associations for construction trades, and it is clear: things will change. Similar to 9/11, this too will pass but likely shift our landscape forever. Most likely, those who fail to adapt will suffer. Some changes will be dramatic, others subtle, but at the end to this decade, they will all be clear to us. The question is, what will we be saying as we look back? Did we see the trend shifts and make the required adjustments? I hope you think seriously and agree we need to be on it or get run over. The Code Update section is an excellent example of changes likely to come.
It is not all bad news. The SMA board has been on the forefront to make industry changes, not to survive but thrive in the coming decade. This newsletter will focus on the various SMA programs. Some are in place, like the Silica Compliance Program; others are new and just kicking off, such as the SMA Stucco Training Modules and the SMA Contractor Certification Program. We will also introduce you to the SMA Quality Assurance Program that is under development. This newsletter will cover each program and be your guide to where the SMA thinks the industry is going and how the SMA can help your stucco and your business succeed.
The SMA plans a Webinar soon to explain these programs in greater detail and answer member questions.
SMA Silica Compliance Program
The SMA Silica Compliance Program continues to be an industry-leading program. Respirable silica dust is a serious issue. Just as serious is the employer’s responsibility to protect their employees. The SMA has a proven written exposure plan for your company – specific to plastering and adhered masonry. Our YouTube channel has the “Silica Awareness” video covering the minimum items you must cover with all employees. The SMA also offers “Competent Person” training and a card to verify the training. All in the Silica Program is FREE to SMA contractors, including the required written exposure plan, the toolbox talk sheets in English and Spanish and the training we offer with testing. Consider the SMA Silica Program similar to auto insurance. Getting in after an OSHA fine is the same as asking your agent for insurance after the auto accident, too late now. Being an SMA member helps protect you.
Why a Stucco Training Program?
Why do we need this? First, it is still a free country, and no one will force you to anything against your will. But most seem to agree, we do not have the training programs required, and while these may not be perfect, they are a good start.
Stucco market share grew and then suffered a setback with leaky buildings. Of course, all buildings leaked, but stucco was an easy target for litigation. Not all regions of the country were impacted equally, nor are the after-effects the same. Why?
- Stucco is easy to attack because it is site fabricated.
- Stucco has more variables than other claddings.
- The industry has lacked a collective voice and fragmented.
- We have some bad actors out there. And since low bid is king, they can continue.
- Codes and standards are changing fast, making it hard to keep up.
The result is stucco is the easiest cladding to attack and hard to defend with mixed messages, codes changing as fast you can blink. The workers in the field hardly stand a chance, as well as the supervisors.
The SMA set out to help with one voice, acknowledging regional allowances for the industry and a solid defense plan. The SMA has put the modules (classes) on the new SMA YouTube channel. Clicking like and subscribing helps the SMA and the industry be a collective voice. The first step is simply a couple of clicks that cost us nothing; we hope you start there to help our industry.
SMA Online Video Training:
Modules 1-5 – Lath & Plaster
The SMA Online Video Training has five 30-minute training modules on lath and plastering. Modules 1 and 2 are lathing, 3 is material, and 4 and 5 are plastering. It is NOT merely code memorization; these are trade tips for the workers in the field. The SMA believes it is critical that trade workers understand the WHY. Why lap housewraps/paper to flashing and how? Why you should counter flash kick-outs? Why hard float the brown coat? We also include trade tips, such as cutting casing beads more efficiently, improving production using the hawk and trowel, and how to cut angles in wet cement plaster. Module 4 covers the plaster pumps, different types, how they work, and tips on using these production masters. Module 5 covers the finish coat. Focus is devoted to doing a quality smooth trowel cement finish.
Overall, these modules will be great for those getting started in lathing and plastering as well as seasoned pros. They are all free to the public on the Stucco Manufacturers Association YouTube channel and on our website.
For those wanting a training card to verify taking the class, the SMA can offer a picture card with an SMA registration # after passing a 50-question test on the website. The processing fee is $75 per test. If a person wants to take lath and plaster (100 questions), the fee is $100. We allow a person, should they fail, to re-take the test at no extra charge, but they must wait 30 days. The courses passed are listed on the back of the card.
Module 6 – Supervision
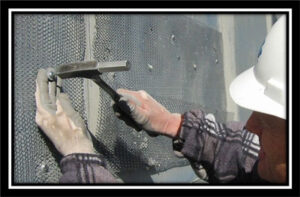
This is the SUPERVISOR course. The Supervisor course includes Modules 1 through 5. Module 6 (Supervisor) includes a manual for lath and plaster supervisors and is the gateway to certifications. This course material covers leadership skills, documentation of events, building science, and how to use SMA technical bulletins to do better stucco and protect the building owner and the contractor. Supervisor training/education has never been available to the stucco industry. The course material has been vetted by experts in defect litigation, building science, and leadership skills, with a focus on lath and plastering. Module 6 is the gateway to SMA Contractor Certification.
SMA Contractor Certification
The first requirement of the SMA Contractor Certification is to have an SMA supervisor on staff. The process verifies the leadership has been trained and educated on lath and plaster. A contractor can send an employee or take the test themselves. If the SMA supervisor leaves, certification will follow that supervisor. Contractors should consider who they want to have approved. SMA Contractor Certification requires being in business for over two years with verifiable references and includes a background check. Approval is by the SMA Board of Directors, and the board can revoke certification. The cost is $500 for SMA members. However, to thank our contractor members, the SMA offers to put the $500 certification fee toward your next year’s annual dues. This essentially means it costs current SMA contractor members nothing to get certified. It is the board of directors saying thank you for supporting the program and the SMA. Upon approval by the SMA board, the contractor can use the “Certified” logo on letterhead, equipment, or other approved places. An SMA letter will be sent to verify you are SMA certified that you could use to submit with bids. Certification demonstrates your company is a step above the competition. Because the low bid is not a fair selection process. Non-SMA members can become certified for $1495.
SMA Quality Assurance Program
This program is currently under development. The concept is pretty simple. The SMA Certified Contractor will receive forms and checklists that they may use. The program is not mandatory. The form verifies materials, flashing, and procedures, with room for comments and pictures. The report can be printed and given to the building owner. The report can be used later should questions arise, particularly when the building is sold. The report can provide future inspectors a comfort level with what you did under the stucco.
Besides sending this to the building owner, a copy may be sent to the SMA vault. The SMA will keep these reports for ten years. At that time, the statute of limitations expires, and records are far less critical. Should a consultant opt to file a lawsuit against the SMA Certified Contractor who has put in a file for that project, the SMA will have a record and provide comments as an authoritative source on industry practices. The SMA opinion can help contractors and their insurance carriers better protect them against frivolous lawsuits. For those worried about the program, it is 100% voluntary, but taking pictures (which the SMA recommends, which locations to take them) can often help contractors spot minor defects as well, allowing them to make needed adjustments. If work under the stucco is done per industry practice, this evidence can provide a strong case that intrusive investigation is not warranted. Because once they start cutting into the stucco, it tends to be a point of no return. The forensic group will tend to want to justify the reasons for cutting into the stucco. The report (pictures) can help identify errors, be a good defense and provide a comfort level to others.
CODE UPDATE: ALL ABOUT THE WRB
For decades it was pretty simple for plastering contractors; we all used asphalt-treated kraft paper water-resistive barriers (AKA “black building paper”). We knew there was a Grade D for stucco, and it could be 10, 30 or 60 minute-rated. We also knew we had to put two layers over wood-based sheathings. Get the laps right, and you’re good to go. That world is long gone. Today there is a mind-numbing amount of selections of WRB products, and the codes have changed significantly. You need to read and understand this.
COMMERCIAL
International Building Code (IBC) section 2510.6 (commercial) has replaced the term Grade D with ASTM references. Grade D is now referred to as compliant to ASTM E 2556. Type I is 10-minute, and Type II is 60-minute Grade D.
2018 Code: 2510.6 Water-resistive barriers.
Water-resistive barriers shall be installed as required by Section 1403.2 and, where applied over wood-based sheathing, shall include a water-resistive vapor permeable barrier with a performance at least equivalent to two layers of water-resistive barrier complying with ASTM E2556, Type I. The individual layers shall be installed independently such that each layer provides a separate continuous plane and any flashing (installed per accordance with Section 1404.4) intended to drain to the water-resistive barrier is directed between the layers.
SMA Policy: This language, while well intended, is confusing and not always possible when two layers of water-resistive barrier are applied and integrated with flashings. Besides making it virtually impossible in cases to fully comply, double-layer kraft paper has been used for several decades with no evidence that this method of application has been an issue for water intrusion. Fortunately, there are 2 (two) exceptions to the above code requirement that provide relief and options.
Exceptions:
1. Where the water-resistive barrier that is applied over wood-based sheathing has a water resistance equal to or greater than that of a water-resistive barrier complying with ASTM E2556, Type II and is separated from the stucco by an intervening, substantially nonwater-absorbing layer or drainage space.
2. Where the water-resistive barrier is applied over wood-based sheathing in a Climate Zone 1A, 2A or 3A, a ventilated air space shall be provided between the stucco and the water-resistive barrier.
Exception 1: The SMA sees this as primarily allowing one layer of water-resistive barrier to be substituted for rigid foam or a drainage mat. We fully support this option. One-coat stucco has been doing this for decades with great success. Some experts feel that this excludes asphaltic paper. The SMA does not agree and states that asphaltic kraft paper (Grade D) absorbs “minor” amounts of water, enough to wrinkle, but do not “substantially” absorb water. To verify this claim, if substantial amounts of water were absorbed into the kraft paper, the thin scratch coat of fresh cement would never cure as too much water would be taken from the cement. Flash drying in cement scratch coat occasionally occurs, but only in hot, dry, and windy weather. It is the weather that dissipates the moisture. This means the separate layer rule is also negated for asphaltic papers. Mixed water-resistive barrier products would require two separate planes. The SMA recommends that these assemblies have the house wrap product applied first and a layer of ASTM E 2556 over that.
Exception 2: These climate zones are established by ASHRAE. In short, they cover most of Florida, Texas, Louisiana, South Carolina, Mississippi, Georgia, Alabama, and parts of North Carolina, Arkansas, Tennessee, and Oklahoma. Your architect/designer should verify the zone. The ventilated space means with assembly requires a drainage mat under the stucco when applied to wood-based sheathings. California is currently exempt, but this requirement for stucco is likely coming in the next few years.
RESIDENTIAL
The International Residential Code (IRC) language on stucco WRBs (section R703.7.3) is very similar to the commercial (IBC) code, except it still references Grade D paper. It also has exceptions as well. Exception number 2 replaces the term “ventilated air space” with a “designed drainage space.” They have also left out any Climate Zone references, thereby adding even more confusion.
The SMA understands that the IBC is intended for commercial structures by covering more relevant buildings such as multistory, hospitals, and schools. The IRC is strictly for duplexes and single-family homes.
This now introduces the term “Drainage Space.” Fortunately, ASTM E2266 is a standard that covers the “drainage wall.” Per ASTM E2266:
A Drainage Wall: is a wall system in which the cladding provides a substantial barrier to water intrusion, but which also incorporates means for dissipating water that may circumvent the cladding. For purposes of this standard a drainage wall is assumed to incorporate a concealed weather-resistive barrier¹ over which drainage, away from water-sensitive components of the wall, may occur. In addition, to drainage behind the cladding, evaporation may play an important role in dissipating moisture in some types of claddings.
This seems to be written to define stucco with building paper over framed walls specifically. The cement plaster, properly mixed and applied, sheds the vast majority of the water. We accept that incidental water can circumvent the stucco and incorporate a concealed water-resistant barrier. Cement stucco also absorbs moisture and dissipates that moisture to the exterior. Some consultants refer to this a “reservoir” cladding. While some think of this as a negative, ASTM E2266 makes it a positive feature as Portland cement, unlike water-sensitive materials, is relatively unaffected by water.
FOAM SHEATHING
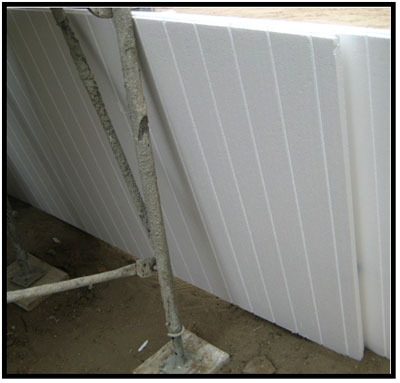
As Continuous Insulation continues to gain favor under exterior claddings, it stands to reason that codes have adjusted as well. Currently, the International Building and Residential Codes have many references to Foam Plastic sheathing; most are about cladding attachment and energy savings.
Exception 1: The code supports the use of rigid foam as replacing one of the two layers of the water-resistive barrier when two are required. While not required by the IBC, it is generally recommended to use a tongue and groove or a rigid board that incorporates drainage channels on the backside. The SMA rationale is that this is required for one-coat stucco through the Evaluation Report(s), and makes sense the commercial code is generally more restrictive due to the structure and occupancy coverage.
Another option is to use a drainage mat behind and the rigid foam to enhance drainage. Drainage between the foam sheathing and cement plaster applied to the foam will not occur. This is noted in the Portland Cement Association (PCA) Plaster/Stucco Manual under Coolers and Walk-in Freezers: “Portland Cement plaster bonds tenaciously to most insulation, such as polyurethane, polystyrene, and cork.” This tenuous bond, while structurally beneficial, will not allow for drainage. The SMA considers bonding of cement plaster to rigid insulation similar to stucco over masonry substrates. This also explains why most plaster bureaus encourage the water-resistant barrier to be under rigid insulation.
CONCLUSION
Always follow what the designer has specified. If you have concerns that the design may not meet code, you should request verification that it does indeed meet current code, but then proceed as directed. NEVER switch out or alter the water-resistive barriers to what you think is code minimum or put in products that you believe exceed the code for everyone’s protection without approval. DO NOT DESIGN: point out potential concerns, use SMA documentation to support your claim, and document the response. Protect yourself.
PLEASE NOTE: SMA OFFICE CONTACT INFORMATION
Mark Fowler, Executive Director
Marlene Lampert, Office Manager
Stucco Manufacturers Association
5753 E Santa Ana Cyn Rd, Suite G-156
Anaheim, CA 92807
Office: 714-473-9579
Mark@stuccomfgassoc.com
Marlene@stuccomfgassoc.com
REMEMBER: The SMA has a fairly large library on all things stucco. Members of the SMA are encouraged to call the SMA office if the staff can be of any assistance.