MESSAGE FROM THE SMA EXECUTIVE DIRECTOR
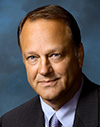
Mark Fowler, SMA Executive Director
The SMA has been busy and been invited to present in Texas and Florida. There is a definite vibe in the lath and plastering industry that change is needed. At one time there were many associations and bureaus dedicated to promoting lath, plaster and stucco. These groups used technical excellence and promotional plans targeted to promote the more expensive and superior finish materials in the plaster family. Today only a handful are left, and most have become more focused on drywall — and even gone as far as shifting promotional efforts more toward metal or other paneled exteriors.
Lath & plaster is not the lowest cost or simplest installation for the construction industry. While cement stucco is considered a staple in the southwest, it is a premium in most regions of the country. Significant loss of stucco marketshare in California or Arizona seems unlikely to occur. However, we should not forget that 40 years ago, tract homes being built by non-union labor was inconceivable to us in the industry, but that did come to pass.
The point is that plastering needs promotion. Consider that drywall ads are run in current architect magazines and we see none for plastering. Maybe the lath & plaster industry should take a cue from the same industry that kicked them to the curb only a few decades ago. Taking a market for granted is one of the most common errors an industry can make until it is too late. The good news is that designers and building owners want plaster. The SMA knows this to be true as we receive phone calls and emails requesting help with design, details and product selection on a daily basis.
As other associations shift their focus away from lath and plaster to drywall and exterior panels, the design and even code enforcement entities have fewer and fewer resources for help. The SMA is not funded through a collective bargaining agreement that creates an unstoppable and continuous source of revenue. Marketing is not by accident; it requires planning and funding. The alternative is a slow demise in market share. It is our collective duty to find ways to deliver lath & plaster to the end users at a reasonable cost and then ensure they want it again on the next project. The simple translation is to service the designers with credible expert advice, supply a skilled work force, and assure quality–all for an affordable cost to building owners. The good news is that the vast majority of designers expect to pay a slight premium for lath, plaster and even quality stucco. Recent stories out of the East and Gulf Coast suggest that trouble is brewing for the entire plastering industry. Ironically, it appears the time we might need those old plaster bureaus the most is when they are systematically being destroyed.
Much of the lath & plaster industry is aware of a crisis, and making moves to save plastering is being discussed. This includes groups like the Texas Lath & Plastering Contractors Association, the National One Coat Stucco Manufacturers Association and the Florida Lath & Plaster Bureau. Each has met with the SMA and shared their concerns that cement stucco is under attack. The agreed plan is to address the first need: what can be done to ensure plastering and stucco will continue for the next generation?
A major concern is the claim about water leaks. While some are real issues, others are tests being manipulated to force leaks, substantiate frivolous claims and secure insurance funds. The SMA has two goals:
- Help those building owners who have had bad stucco installed that resulted in leaks.
- Help those contractors who have installed functional stucco and are being hit with frivolous law suits.
Lath & plaster is skill intensive and requires that unique blend of craft, science and experience to ensure it functions as it has for over 200 years in the United States. We all want cement stucco installed per ASTM and the best practices. We know that most projects are not installed per ASTM literature and that the vast majority of stucco installations are functioning as intended. One issue is that ASTM has problems with allowing regional differences and alternative practices. The SMA recognizes that there are regional practices that alternates should be allowed. The few stucco jobs that are failing are generally the result of poor practices or a failure to ensure the completed assembly is functional as it was designed. We can and must do a better job if we want to keep lath & plaster relevant. This requires a concerted effort, coordination and some funding to help lathing and the art of plastering. It is only your future at stake.
STUCCO LIVE 2019: January 22-25
INFORMA has contacted the SMA to host “Stucco Live” at the 2019 World of Concrete show, January 22-25 at the Las Vegas Convention Center. The World of Concrete is one of the largest construction trade shows in the world. INFORMA discovered that 20% of attendees are interested to learn and see more on cement stucco. The SMA was a natural fit.
The South Hall will have a section dedicated to live cement plastering demonstrations and an SMA booth shared with the Portland Cement Association. We will have educational classes, product information and experts on staff to answer questions. This promises to be a great promotion to designers, contractors and dealers interested in cement stucco. There will be promotional opportunities and space is limited. SMA members will be given the first right of refusal to display goods and services. If interested, you should contact the SMA before we offer space to the general industry.
SILICA UPDATE
The OSHA ruling has been in place for one full year. At the six-month mark, OSHA announced they had issued over 117 citations for non-compliance to the ruling. They further announced that they will be ramping up citations in year two. Most citations were labeled as “serious.” The three most common violations were:
- Failing to have a written Silica Exposure Plan: All employers must have a written plan and it should be specific to the tasks the employees perform.
- No test data: OSHA inspectors are charged to verify the employers have tested the tasks employees perform with respect to silica exposure.
- Failing to follow the written plan: The written plan will include Table One and states what employees must do to avoid silica dust.
To date, there are records of plastering firms cited for silica dust violations. None were SMA members. SMA has been working with various OSHA offices and will continue to improve our members’ written plan to protect your workers and assure compliance to OSHA.
OSHA has also announced plans to expand Table One. This means that new tasks will likely be added. The SMA has also continued testing silica as it relates to mixing mortar and will be updating the written exposure control plan for SMA members to use as required by OSHA updates before the end of the year.
SMA contractor members may also request online “Competent Person” training. Contact the SMA to arrange for your foreman to receive their important training. [Click here if you need additional information about the SMA’s Silica Compliance Program.]
SMA GOLF TOURNAMENT
On September 24, the Annual SMA Golf Tournament was again held with the biggest turnout to date. Members enjoyed perfect weather, a private country club, and food that included a carving station and a taco bar lunch.
The raffle garnered some of the most excitement of the day. Prizes included high-end sipping tequilas, a Playstation 4, gift cards for dinners, Fitbit, even a large 4K television. Many commented that the SMA has the most impressive raffle prizes of any tournament. We can thank our great sponsors for their generosity that allows the SMA to supply such an impressive list of prizes. We are certain next year will again be a banner year.
SMA MEMBERSHIP MEETING
The SMA November 7 meeting will feature an expert on the construction economy with a strong focus on housing issues. Sign up online today.
Feature Articles
HOW LONG WILL STUCCO LAST?
There have been groups that try to determine the life expectancy of various claddings. The US Department of Energy through the BEES (Building for Environmental and Economical Sustainability) will be adding to their software programs updated information regarding cement stucco as an exterior cladding. The report states “A properly installed stucco exterior will have a useful life of 100 years.” This powerful statement from the US Government was the result of data collected through exhaustive research and can be used by designers and insurance companies. There are countless framed structures in the United States that are 100 years old and clad in cement stucco.
Ironically, 100 years is almost laughable to those in Europe. They have used stucco for centuries with a very long history of success. If you get the chance to travel old central European cities, you will note that many of these structures display the year they were built and subsequent renovations. Unlike the new world of America, renovations are not every decade, but typically about once every one hundred years.
It is not uncommon to see buildings painted elaborately to highlight how old they really are. For an American, we have to realize that many of these structures pre-date US history. Cement stucco has been the unquestionable cladding of choice for most of Europe. The weather-resistance, aesthetics and proven durability continue to make stucco the cladding of choice in Europe. In speaking with locals, they have seen an increase in other panelized claddings and note that they will not last like stucco and must account for the shorter life span.
The collection of the dates on various buildings in Germany should prove that cement stucco can and will last a very long time indeed. Even over framing the force of the United States Government proclaims cement stucco will last 100 years. The SMA is in agreement, and the key is to have stucco “properly” installed. Properly means that cement stucco must function and two major factors addressed:
- Stucco must act as a weather barrier: This means good product selection that is mixed and applied to resist climate and water penetration. Cracking is minimized and protection increased. It is not impossible or even expensive to make this happen. The Europeans have been doing it for centuries.
- Stucco must be flashed: If the cement stucco works as a weather and water-resistant cladding per item #1, it makes sense that flashing is critical at termination and penetrations subject to water entry. Water entry must be controlled to allow only “incidental” moisture intrusion. This also includes penetrations, like windows, that are properly rated to keep water out. Again, Europe has been doing this for a very long time. In fact, their windows are in general superior in many ways to the new world windows we use. They expect windows to last a hundred years until the next renovation.
While the list for an inspection of lath and plaster could be long and detailed, it is predominately these two items that will make it work or fail.
THREE THINGS THAT MUST CHANGE IN STUCCO
Cement stucco is historic and unique as noted. The lather and plasterer must know what will and will not cause issues. They must know materials and how to blend them correctly. They must install lath and stucco to look good and function as the owner expects it to. While some believe following ASTM, the Code or some publication is the key to success, the truth is cement stucco is somewhat forgiving. This explains why it has worked for decades, or even centuries in Europe.
Experts have seen stucco installed in ways that make them scratch their heads and wonder how did that not fail? Perfection is unobtainable and even the old timers in the stucco industry did things that were not exactly per ASTM, but the stucco worked. A future article should be the noted failures to follow ASTM standards in Europe, yet the stucco still works. This is not meant to provide an excuse for not following ASTM or the code, but it does prove that trade skill and knowledge is still the best assurance for a successful stucco cladding.
Issues arise when skills/knowledge diminish in concert with downward pressure on pricing. This is especially true in price-sensitive markets where saving a few dollars can make or break the plastering contractor. However, there is always a point where cutting corners can result in failure. The following three items are considered paramount by most experienced stucco experts. All three are noted in ASTM in some form or another. To stave off issues, it is important the lath and plastering contractor understands and can overcome these three obstacles to functional stucco.
-
The tan metal cap flashing leg is reverse lapped to the building paper under the lath. Water may be directed into the structure. A simple oversight may result in big problems. REVERSE LAPS: We install shingles on the roof from the bottom up to meet the “ Shingle-Effect.” Yet, on walls we seem to lose sight of that concept. Water drains down. Lower layers must be lapped by the upper layers. This concept extends to integrated flashings as well. It is not uncommon for a wall leak to be traced back to a reverse lap. Since only incidental water should find its way behind the cement stucco membrane, most water will be absorbed into the cement and harmlessly exit as a vapor to the exterior. However, on occasion, more than incidental water may get in, weep or drain down, and the “reverse lap” is the path into the wall cavity. Even with a rain screen design, any reverse lap is a potential death sentence.
-
Trowel application allows for better encapsulation of the lath than a tool known as the slicker. THE SLICKER: This is a tool that has been around a long time. It has been called by many names across the country: Go Devil, Cheater or Shahalee are but a few. Using the slicker to smooth the cement plaster is not an issue. It is when it is used to apply the cement to lath that issues arise. The cement must be applied with sufficient force to embed and sustainably encase the lath. The Slicker is often used to scoop large amounts of cement from the mud board to the wall. The weight of the tool with cement makes it hard to physically force the cement in with the required pressure to fully embed and sufficiently encapsulate the lath. It is impossible to work a full day using this tool to embed the cement properly. The result is the lath on the back side of the cement is susceptible to premature rusting and failure. The situation is worse when using a metal lath. It is not a metal lath issue, but an application of cement issue. Cement should be applied with a hawk and trowel or a machine pump designed for plastering.
-
The floating process on the basecoat is to consolidate and densify the cement membrane. BASECOAT CONSOLIDATION: The cement membrane must resist water cracking and water penetration. This requires the cement basecoat to be floated with a wood, cork or other proper float. A sponge float lightly passed over the basecoat coat will bring out some sand and look very nice, but does not consolidate the basecoat. The result is more shrinkage cracking and less resistance to water penetration.
The proper materials, mix ratios and application are critical to a cement stucco that functions. Most plaster experts will agree, these three issues are far more critical than control joint placement, adding rainscreen or other red herring issues.
PLEASE NOTE: SMA OFFICE CONTACT INFORMATION
Mark Fowler, Executive Director
Marlene Lampert, Office Manager
Stucco Manufacturers Association
5753 E Santa Ana Cyn Rd, Suite G-156
Anaheim, CA 92807
Office: 213 379 5890
Mark@stuccomfgassoc.com
Marlene@stuccomfgassoc.com
REMEMBER: The SMA has a fairly large library on all things stucco. Members of the SMA are encouraged to call the SMA office if the staff can be of any assistance.